Introduction
When it comes to manufacturing, two major players in the game are injection molding and 3D printing. Both have their own strengths and weaknesses, making the choice between them a critical decision for achieving the desired results efficiently and effectively.
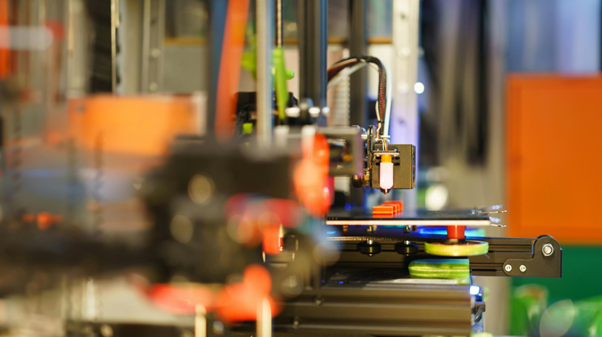
Understanding the differences
Process:
Injection molding involves injecting molten material into a mold cavity, where it cools and solidifies to create the desired shape. It’s perfect for high-volume production, whereas 3D printing, also known as additive manufacturing, builds objects layer by layer from digital designs. This makes it ideal for rapid prototyping and small-batch production.
Materials:
In comparison to plastic injection molding, which provides a diverse array of material options including thermoplastic and thermosetting polymers to meet the needs of various industries, 3D printing has expanded its material palette to include plastics and metals, although its selection remains comparatively narrower.
Complexity:
3D printing shines in producing complex geometries with intricate details, which can be challenging or impossible to achieve with injection molding. This makes it advantageous for prototyping designs with intricate features or customized components. Injection molding, while highly efficient for large-scale production, may struggle with intricate designs and undercuts.
Cost and time:
Injection molding usually requires significant upfront investment in tooling and setup but offers lower per-unit costs for high-volume production. Conversely, 3D printing typically involves lower initial costs and shorter lead times for prototyping and small-batch production. However, the cost-effectiveness of 3D printing diminishes for larger production runs.
How to choose: Injection molding or 3D printing?
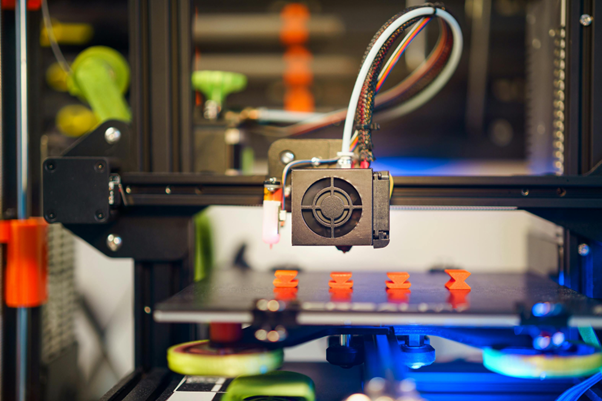
Volume:
Consider the expected production volume. Injection molding is more cost-effective for larger quantities (we consider around 500 units), while 3D printing is preferable for smaller batches.
Complexity:
Assess the complexity of the parts. For intricate designs or prototypes with complex geometries, 3D printing offers greater flexibility and precision.
Material requirements:
Evaluate the material options required for the parts. Injection molding provides a broader range of material properties, including high-performance polymers, suitable for end-use applications with specific requirements.
Lead time:
Determine the urgency of the project. If quick turnaround is essential, 3D printing offers rapid prototyping capabilities, whereas injection molding may require longer lead times due to tooling setup (4 to 6 weeks).
In summary, both injection molding and 3D printing have their place in manufacturing, with each offering unique benefits depending on the project requirements. Injection molding excels in higher-volume production of standardized parts, while 3D printing shines in rapid prototyping and small-batch production of complex designs.
Understanding the differences between these technologies and considering factors such as volume, complexity, materials, and lead time is crucial for making an informed decision tailored to your specific needs.
Feel free to reach out to us here for personalized advice tailored to your needs.