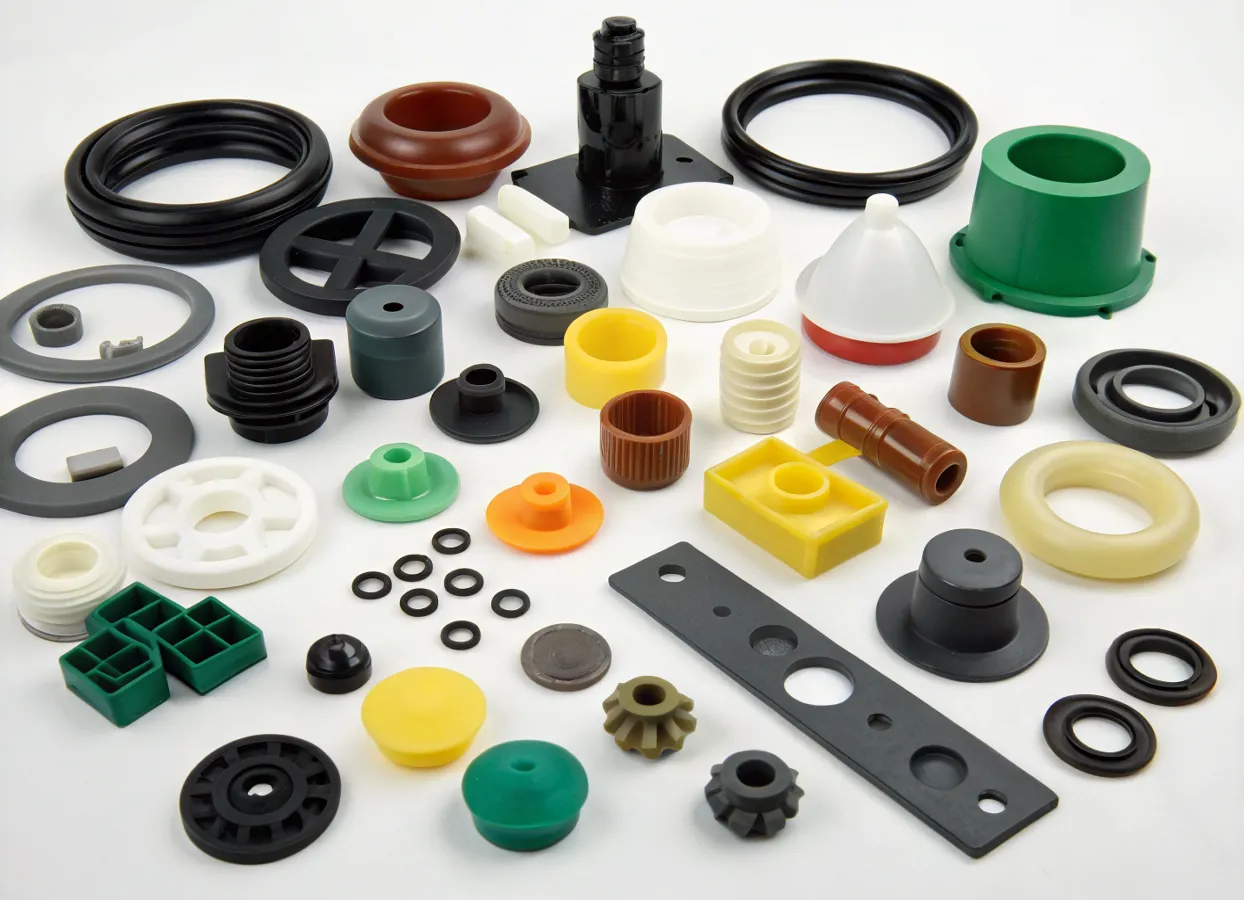
When selecting the best technology for producing flexible plastic or rubber parts, you will often face a dilemma: compression molding or injection molding?
Both processes are among the most popular for manufacturing plastic components, but each offers specific advantages depending on your project’s requirements. To help you make an informed decision, this article compares the two technologies, their differences, and their benefits.
Compression Molding vs. Injection Molding: which Is the best choice for your project?
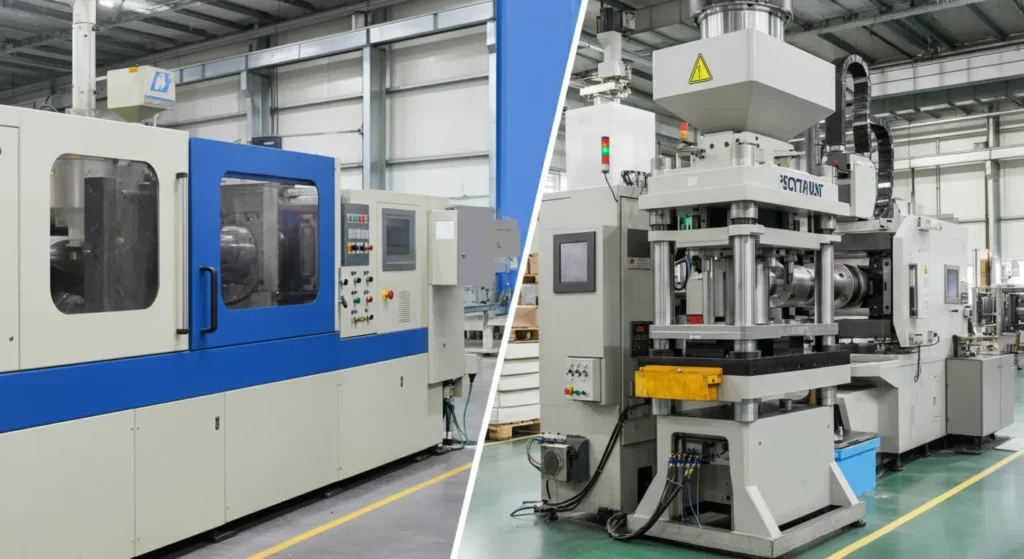
Both processes aim to produce flexible parts, but they differ significantly in their operation. Let’s start with an overview of each technology and the principles that distinguish them.
How do injection molding and compression molding work?
Injection molding
Injection molding is a process where molten plastic, heated to a temperature between 180°C and 250°C, is injected under high pressure into a mold. This method is commonly used to produce high-precision, small-sized parts. Injection molding enables fast manufacturing with tight tolerances and high repeatability.
Compression molding
Compression molding, on the other hand, uses preheated material (typically between 60°C and 80°C) placed in a mold cavity before being compressed under high pressure. This process is particularly suitable for larger parts and materials such as rubber or certain thermoplastics.
What are the key differences between compression and injection molding?
1. Tooling cost and production time
Injection Molding: high initial investment but long-term profitability
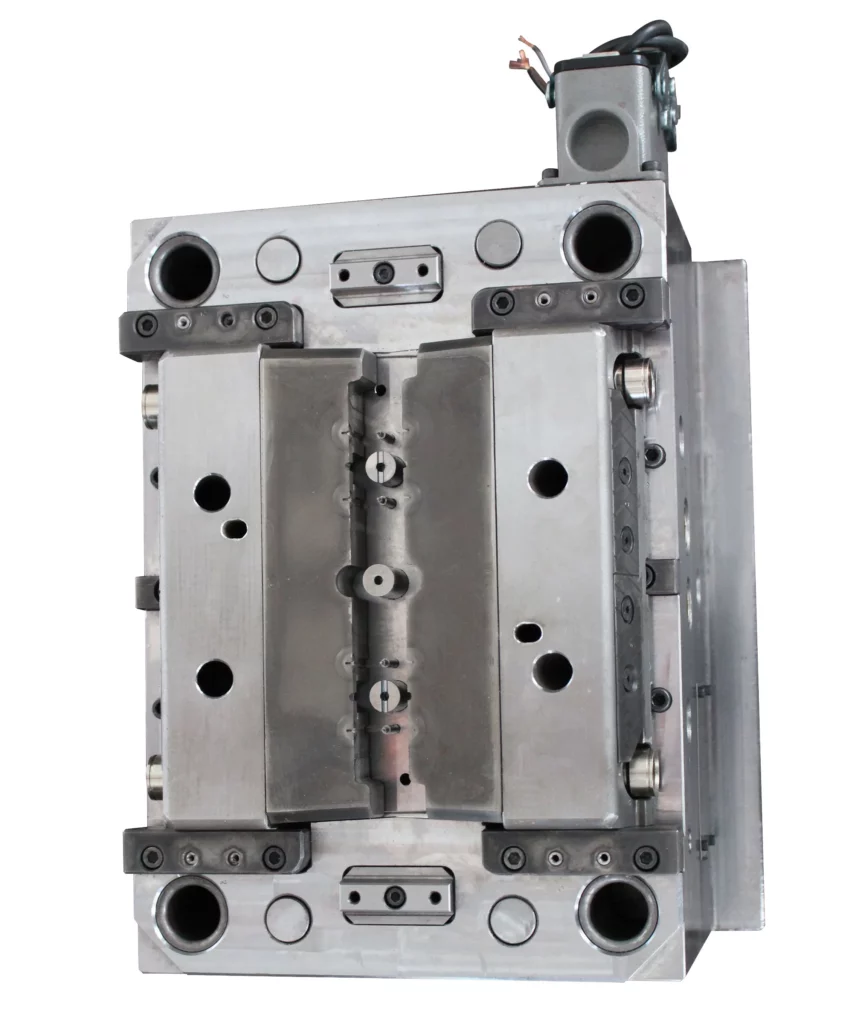
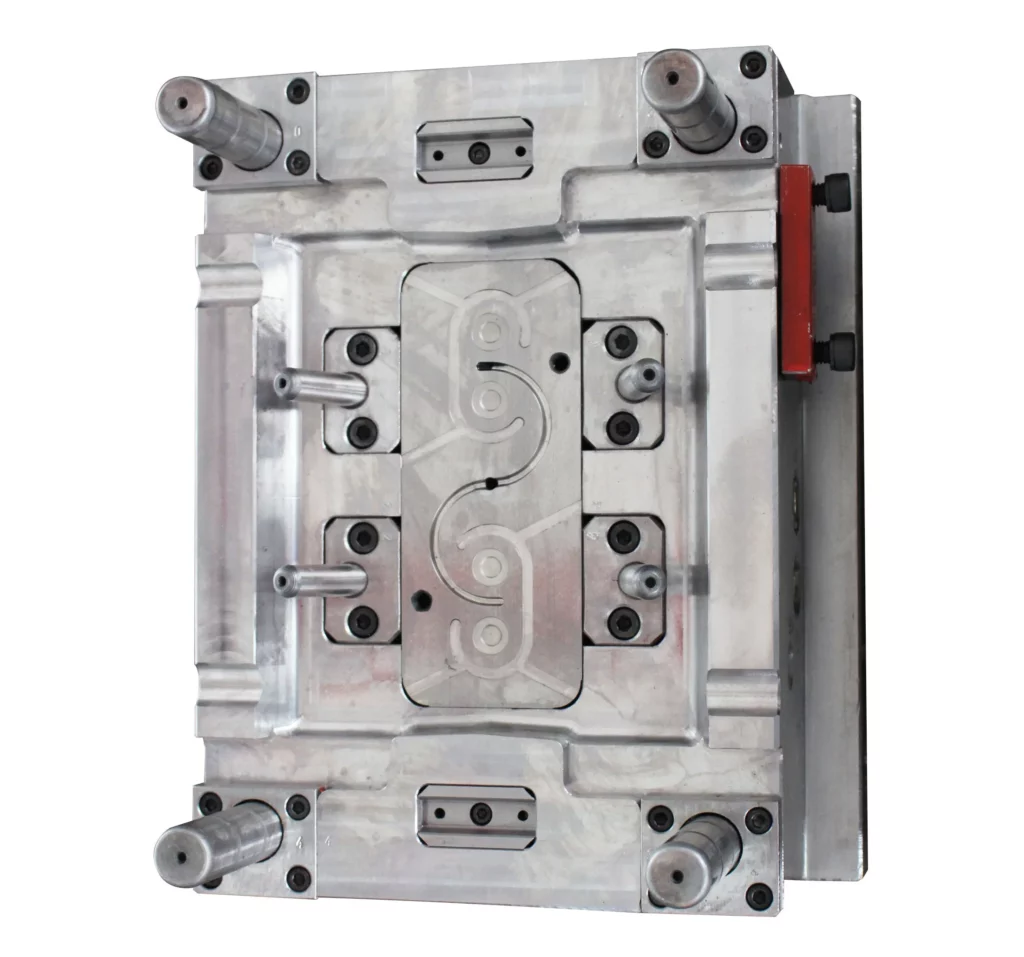
Producing molds for injection molding is a costly and time-consuming process, which can affect production lead times. Depending on design complexity and the number of cavities, the manufacturing of an injection mold can take between 6 to 10 weeks and cost 5 to 10 times more than a compression mold.
These costs include:
- Mold design and engineering, ensuring strict tolerances and repeatable production.
- Complex and precise machining, especially for undercuts requiring mold movement.
However, once the mold is made, injection molding becomes an extremely cost-effective method for high-volume production. Thanks to economies of scale, the unit cost of parts significantly decreases over time.
Compression molding: lower cost and shorter production time
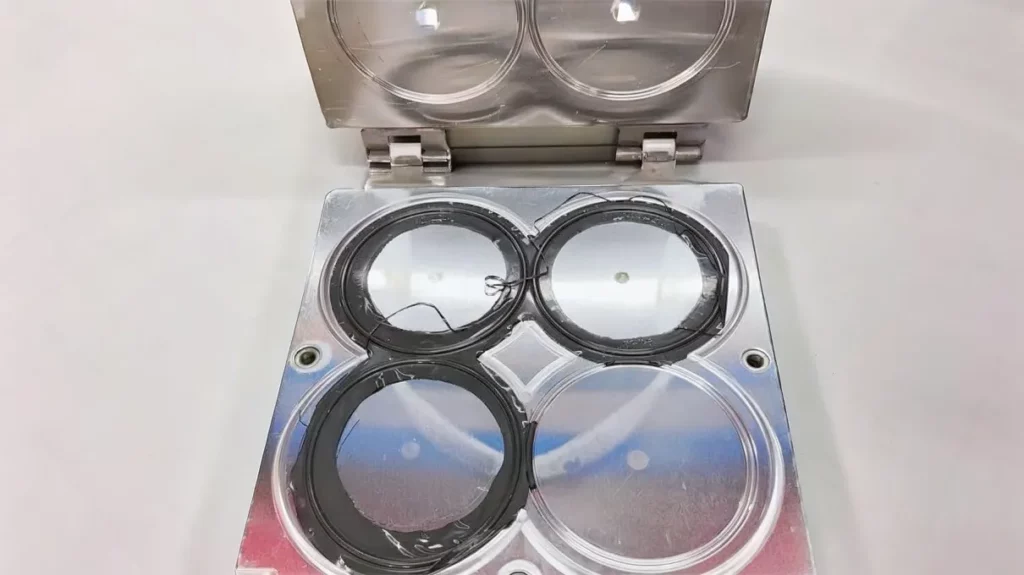
Compression molds are much simpler and faster to produce, with production lead times reduced to 2 to 4 weeks, allowing for faster production launch.
Compared to an injection mold, a compression mold costs 5 to 10 times less, making it a more accessible solution for:
- Small production runs, where amortizing an injection mold would not be justified.
- Large parts, where the mold’s simplicity reduces initial costs.
Thus, while compression molding is more limited in terms of production speed, its low initial investment and quick implementation make it an attractive alternative for certain projects.
2. Part manufacturing time (Cycle Time)
Compression molding production time
Compression molding requires more time due to the heating and pressing process, which can extend the cycle time for more complex parts. Additionally, compression molding involves manual demolding and deburring. In general, production cycles often exceed two minutes, which can slow down the pace for large-volume series.
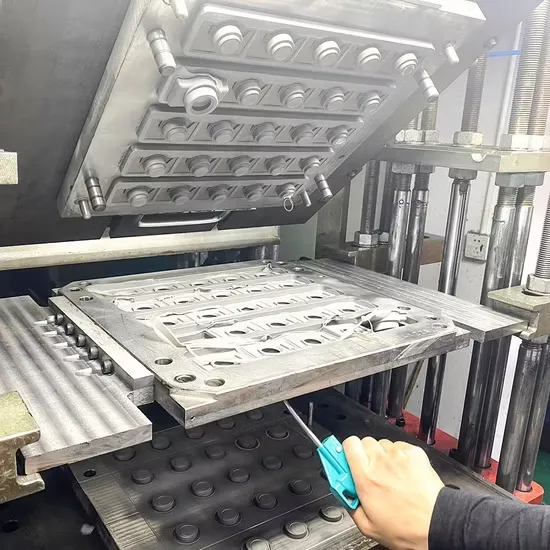
Injection molding production time
Injection molding is a fast and efficient process, with cycle times generally under one minute when automated. This speed allows optimized large-scale production, ensuring high output and rapid manufacturing of standardized parts.
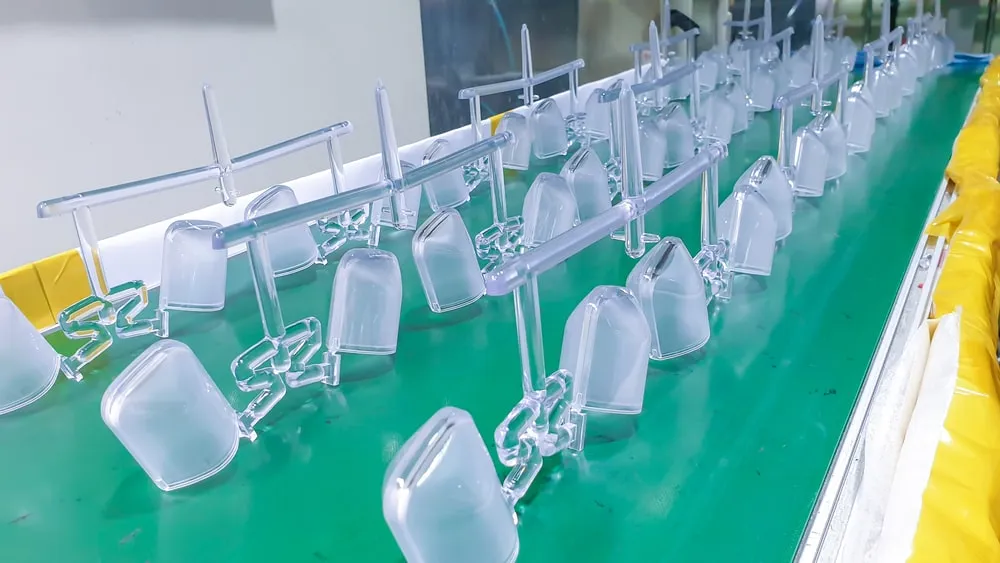
3. Production costs for parts
Compression molding costs
Compression molding can be more cost-effective for small production runs or specialized parts requiring specific materials. However, costs can increase for highly complex parts.
Injection molding costs
Injection molding is more suitable for high-volume production, as tooling costs are relatively high. However, once the tooling is ready, production becomes highly profitable.
4. Materials used
Materials for compression molding
This method is ideal for materials such as elastomers, rubbers, or thermosetting plastics, which require curing to harden and retain their final shape.
Advantages of thermosetting plastics:
- Highly resistant: excellent thermal and mechanical stability, even under high stress.
- Increased durability: unlike thermoplastics, they do not soften under heat, making them suitable for extreme environments.
- Excellent chemical resistance: ideal for applications exposed to solvents, oils, or other aggressive substances.
Materials for injection molding
Injection molding is typically used for thermoplastics, which are melted at high temperatures before being injected into the mold and cooled to solidify.
Advantages of thermoplastics:
- Wide variety of materials: a broad selection of plastic resins (SEBS, TPE, TPU, PU, etc.), allowing customization to application-specific needs.
- Lower cost: thermoplastics are cheaper to produce and process, reducing overall part costs.
- Recyclability: unlike thermosets, they can be melted and reused, making them a more sustainable choice.
5. Design flexibility and part complexity
The design of parts varies significantly between injection and compression molding, particularly in terms of geometric complexity and modification flexibility.
Injection molding: mold constraints
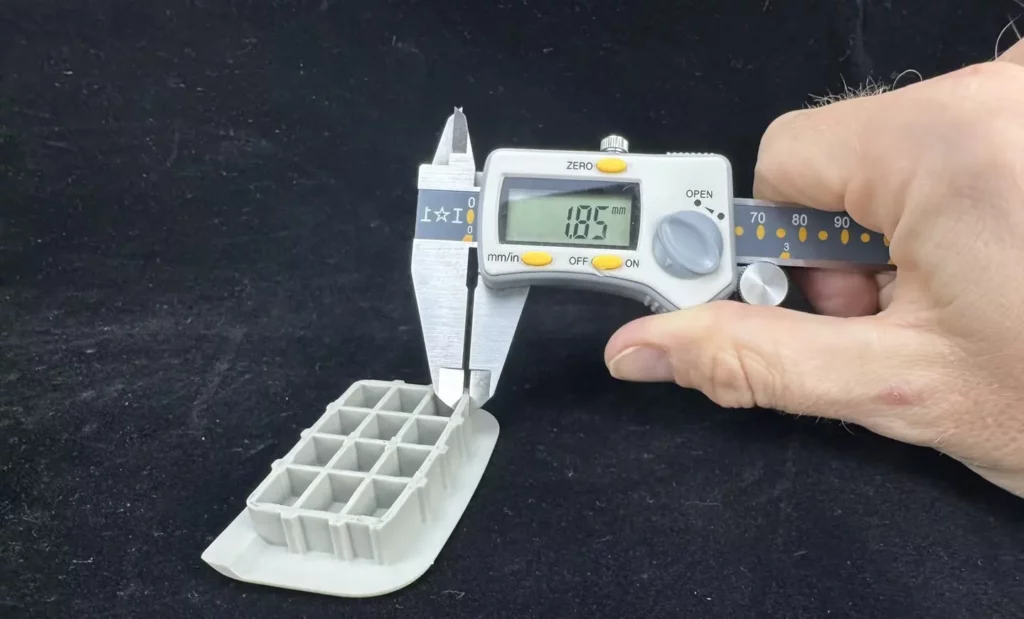
Injection molding imposes strict design rules, especially concerning wall thickness, part geometry, and ejection constraints:
Wall thickness:
- Injection-molded parts must maintain a consistent wall thickness, typically between 2 and 3 mm, to ensure uniform cooling and prevent defects (shrinkage, warping).
- This constraint limits design freedom, especially for parts with significant thickness variations.
Automated molds:
- Injection molding is designed for high production rates, requiring automated molds that do not allow manual demolding.
- Parts with complex geometries, particularly those with undercuts, require mechanical movements within the mold (moving cores, sliders, hydraulic cylinders), significantly increasing costs and lead times.
- Any design modification may require costly adjustments or even the creation of a new tool, affecting production timelines.
Compression Molding: greater flexibility
Compression molding offers greater design freedom, particularly for large and complex parts:
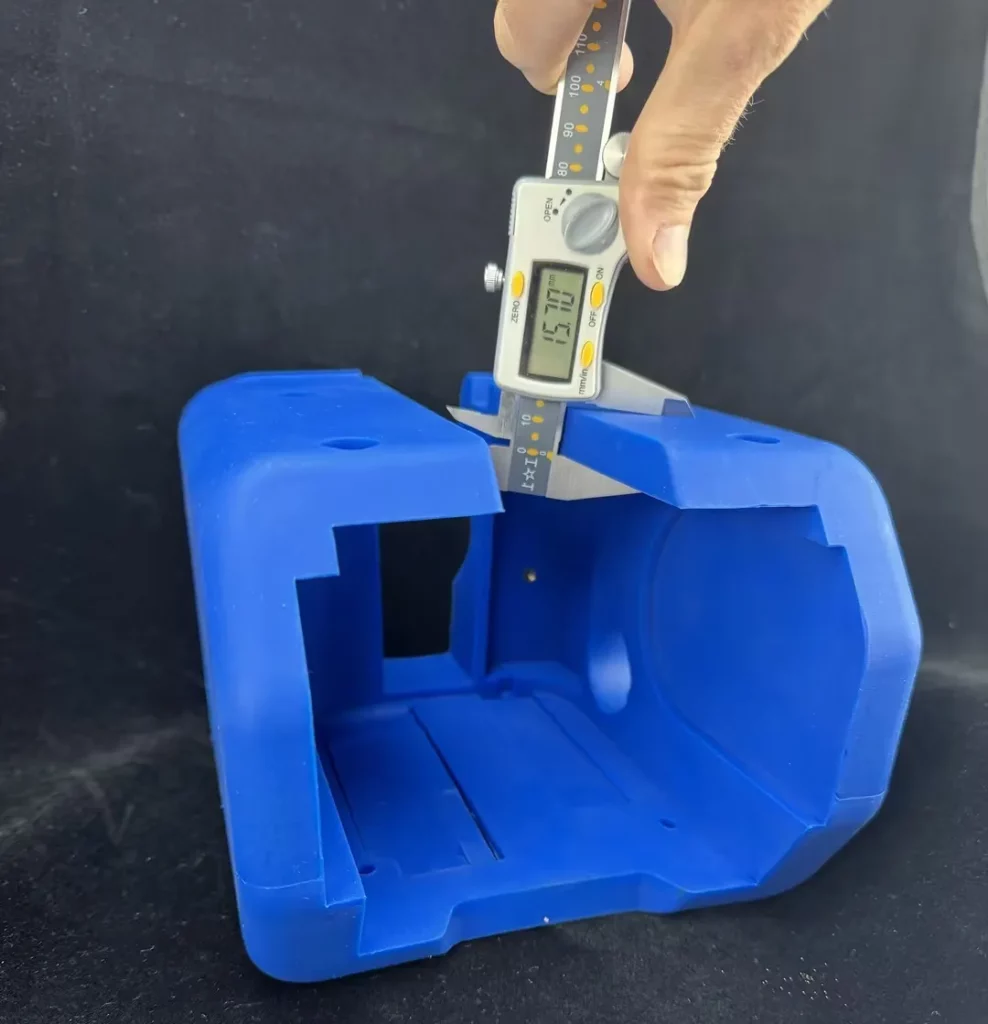
- Wall thickness: unlike injection molding, compression molding allows for thicker walls, up to 10-15 mm in some cases, without significant shrinkage or deformation risks.
- Flexible ejection: compression-molded parts can be manually removed by an operator, eliminating the need for complex mechanisms and reducing ejection-related constraints.
- Easier design modifications: design adjustments are simpler and more cost-effective, as mold modifications are easier to implement than in injection molding.
This flexibility enables late-stage design adjustments, offering better adaptability to project changes.
Comparison table: Compression Molding vs. Injection Molding
Characteristic | Compression Molding | Injection Molding |
Cycle Time | Longer, especially for large parts (measured in minutes) | Shorter (less than a minute), ideal for large series |
Tooling Cost | Lower cost for small production runs | 5 to 10 times more expensive, but cost-effective for large series |
Material Type | Elastomers, thermosetting plastics | Thermoplastics |
Part Precision | Less precise for complex parts | High precision, ideal for thin-walled parts |
Suitability for Large Series | Less suitable for high-volume production | Highly suitable for mass production |
Part Complexity | Limited to simple to moderately complex parts | Can produce complex parts with fine details |
Case Study: Injection Molding vs Compression Molding of Parts
Example of a Part with a Strong Undercut
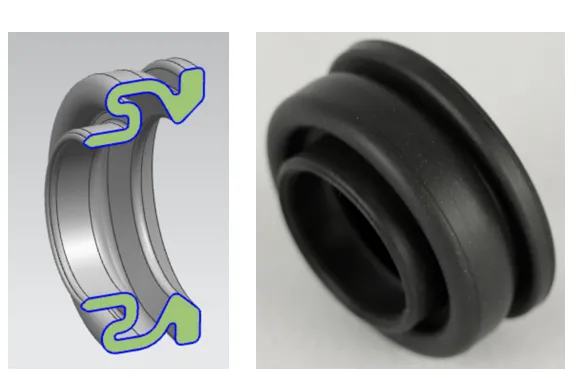
Strong undercuts make the production of this part possible only through compression. Ejection must be done manually, which is not possible with a standard injection mold.
Example of a Part with a High Thickness
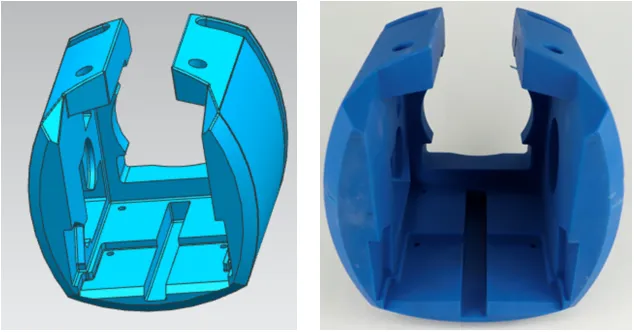
The substantial thickness of this part necessitates the use of compression molding as the production method. With a thickness exceeding 12mm, it is incompatible with plastic injection molding technology, which typically accommodates thicknesses of 2-3mm.
Example of a Part with a Specific Material
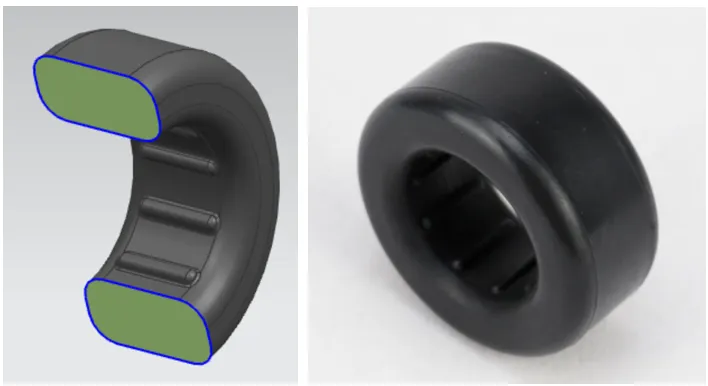
The material of this part is FKM (or FPM), a fluorinated synthetic rubber based on carbon, commonly referred to as fluor elastomer. Its impressive heat resistance allows it to withstand temperatures exceeding 200°C. FPM is also distinguished by its chemical stability, non-flammability, gas impermeability, and good resistance to ozone. This grade of material is not available for injection molding.
Conclusion
Compression molding or injection molding: which technology should you choose?
The choice between compression molding and injection molding depends on several factors, including material type, production volume, precision requirements, and cost. If you need small production runs or complex elastomer parts, compression molding may be the best choice. For larger production volumes and precise plastic parts, injection molding is likely more suitable.
Summary
- Compression Molding: ideal for small batches, specific materials like rubber, and complex geometries with lower precision.
- Injection Molding: perfect for mass production, precise parts, and thermoplastic materials.
Whatever your choice, we recommend working with experts to determine the best method for your specific needs. Contact us today!