Product | Tail light for convertible vehicles |
Technology | Rapid Plastic, Injection Molding |
Material | ABS and PMMA |
Finish | Mirror polishing and Chrome plating |
Timeline | 42 Days for mold, 10 days for parts |
Quantity | 100 sets |
Protolis successfully took on the challenge of reviving an old tail light for this iconic Peugeot model. This was made possible thanks to our multi-material production capabilities, the use of precision ultrasonic welding, and meticulous attention to complex geometries.
About our client
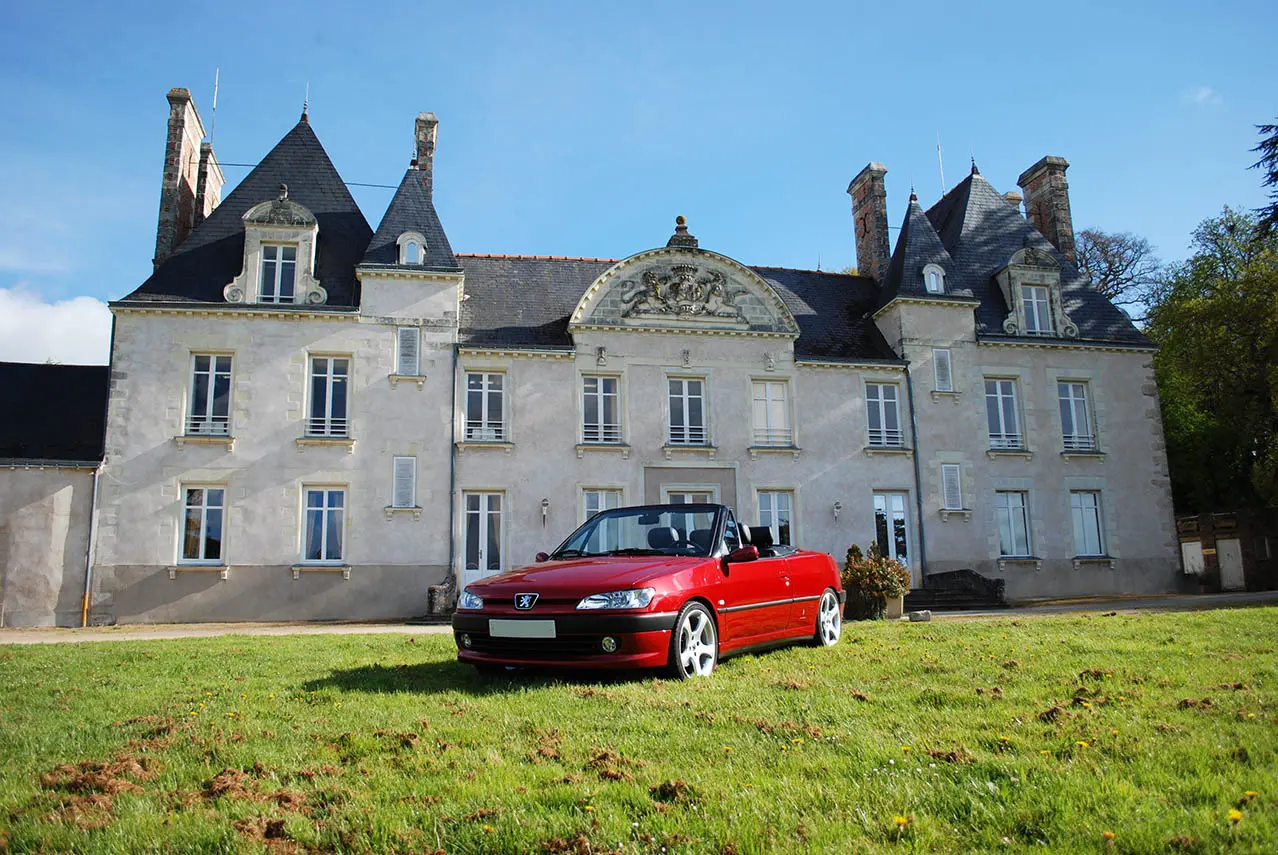
Our customer is an online website specializing in manufacturing unavailable auto parts for the aftermarket.
Project challenges
Cost challenges: Managing costs for intricate parts with diverse finishing requirements, especially for a very limited production run of 100 pieces, presents a significant challenge. Striking the right balance between quality and cost-effectiveness is crucial. At the same time, using prototype molds becomes essential to produce high-quality parts while minimizing tooling costs. This dual challenge demands a strategic approach to ensure optimal results in both cost control and mold efficiency.
Diverse finishing requirements: This project required a mirror-polish for the lenses, chrome plating for the reflective surfaces (such as the inside of the tail light), as well as the creation of a logo in relief. The diversity and precision required for these finishes added an extra layer of complexity to the project.
Assembly of three components: Assembling the three components, including welding a seal using ultrasonic weldings, adds an additional layer of complexity. Ensuring a seamless integration of the box, reflector, and lens was crucial for the final product’s integrity and functionality.
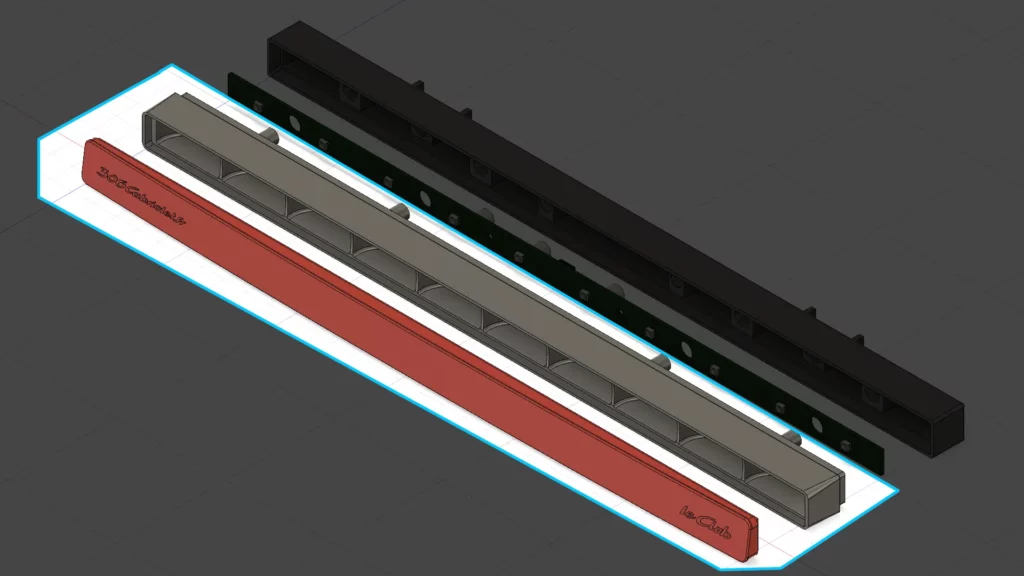
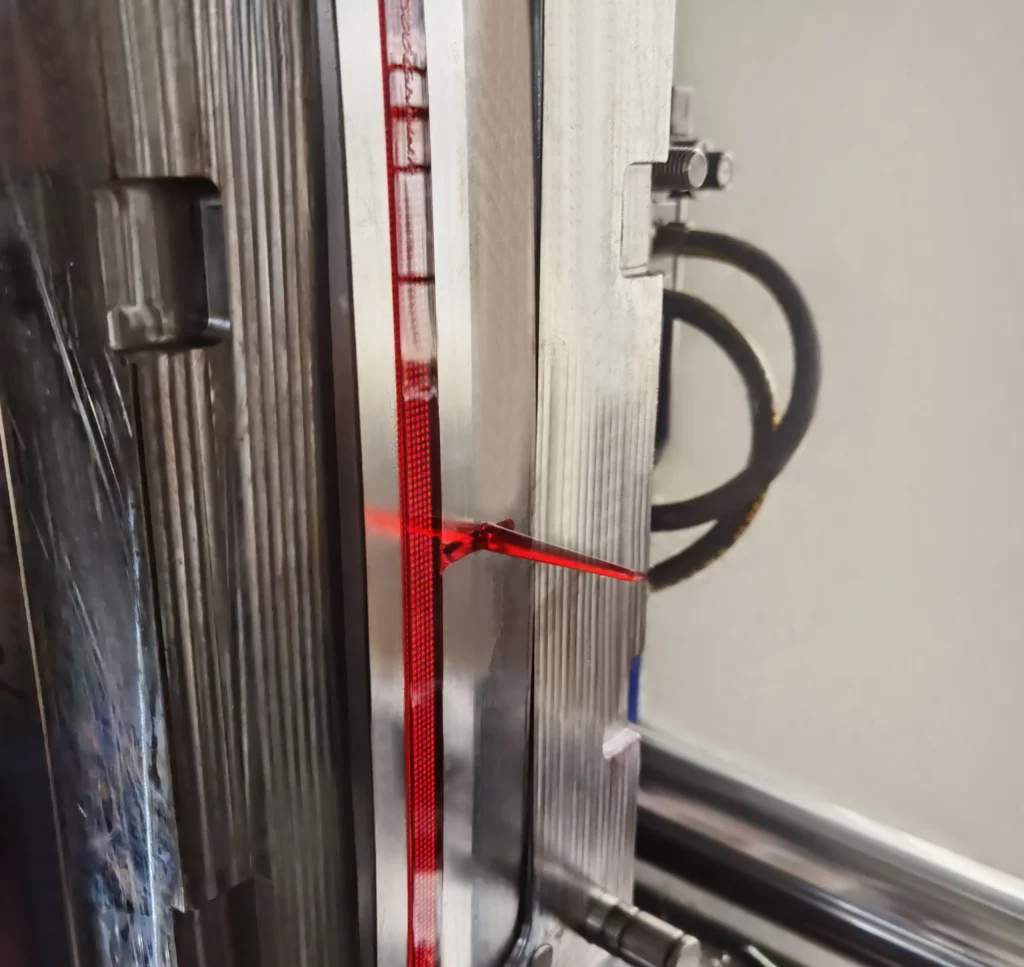
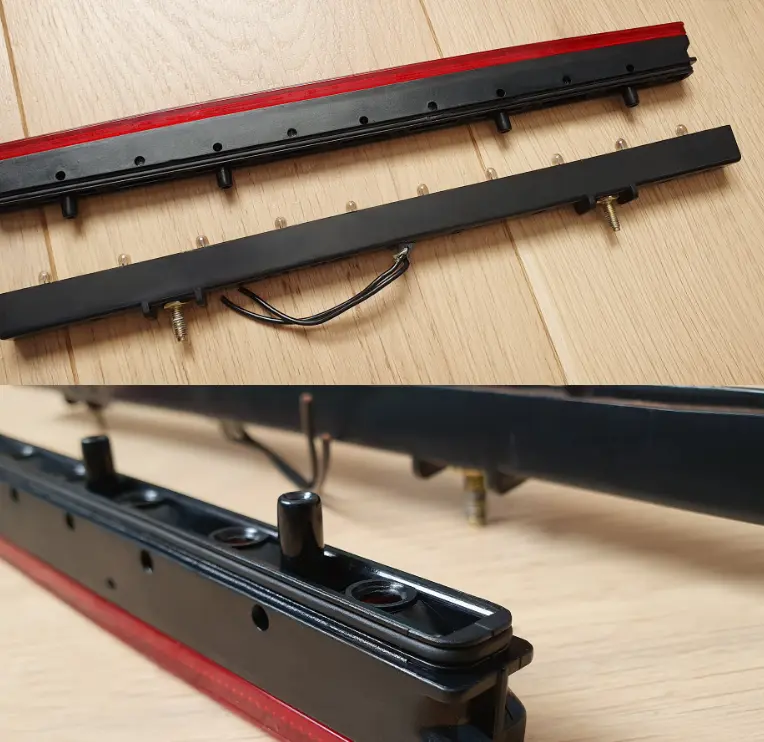
Our solutions
Protolis addressed above challenges through a strategic and innovative approach, implementing the following solutions:
Multi-material assembly: The product have three components, two ABS, and one PMMA, necessitating precision in design and assembly.
Ultrasonic welding integration: Ultrasonic welding is a process that uses high-frequency sound waves to bond plastics by applying pressure and generating heat through friction. Designing suitable locations for ultrasonic weldings is crucial to ensure a secure fit between the PMMA and ABS parts.
Precision in complex geometry: The intricate structure with numerous holes and ribs demands precise positioning to avoid any deviation that could impact the overall assembly.
Diverse surface treatments: Mirror polishing , followed by chrome plating and black spray painting on ABS parts, adds complexity. Skilled artisans are essential to maintain quality.
In conclusion, we are proud to have contributed to this challenging project, reviving a vintage Peugeot tail light. Our advanced production techniques, such as ultrasonic welding and multi-material assembly, have proven highly effective for limited production runs. These methods are well-suited for niche markets and custom-made parts, providing solutions for projects that demand precision in low-quantity manufacturing.
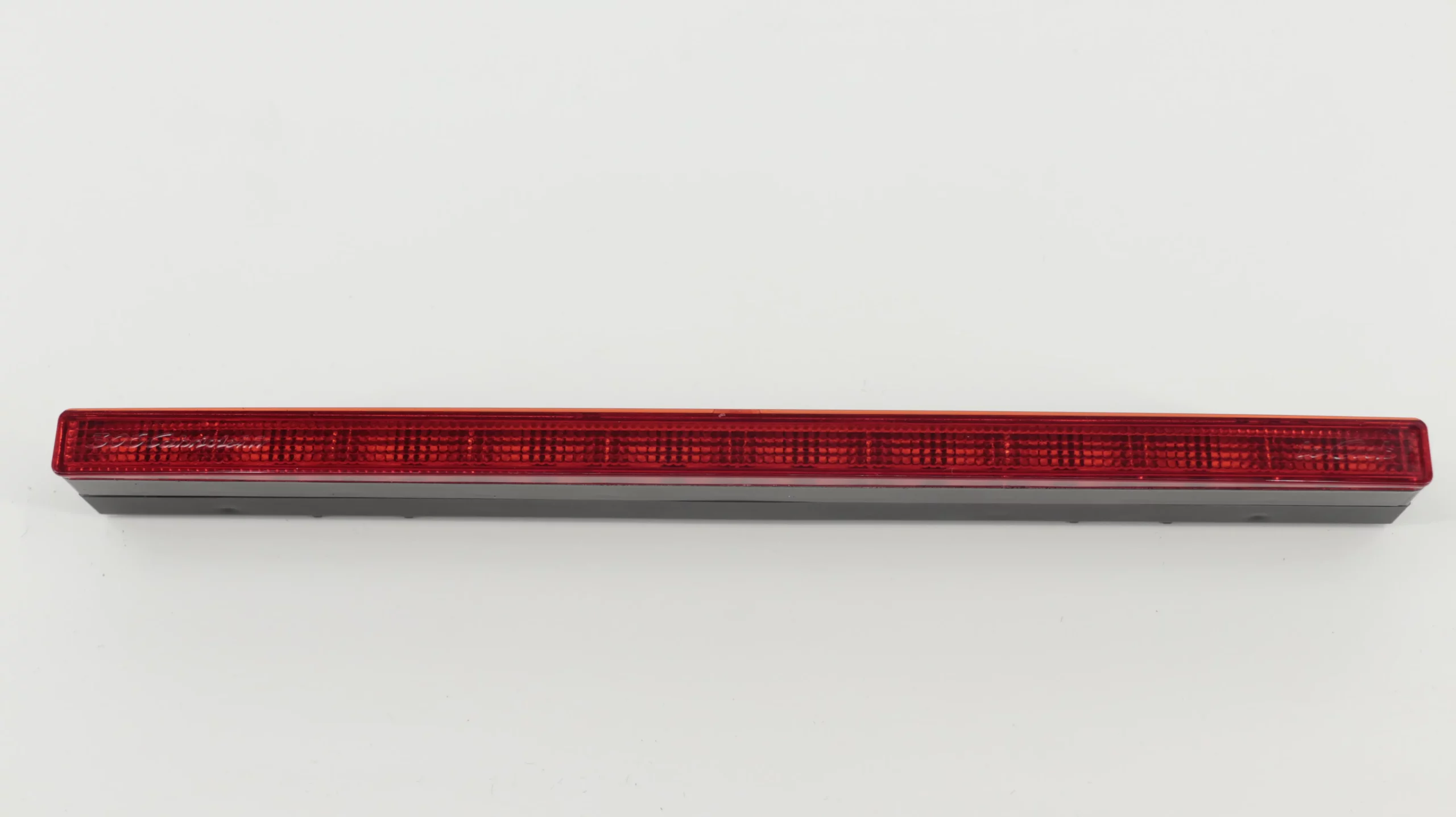
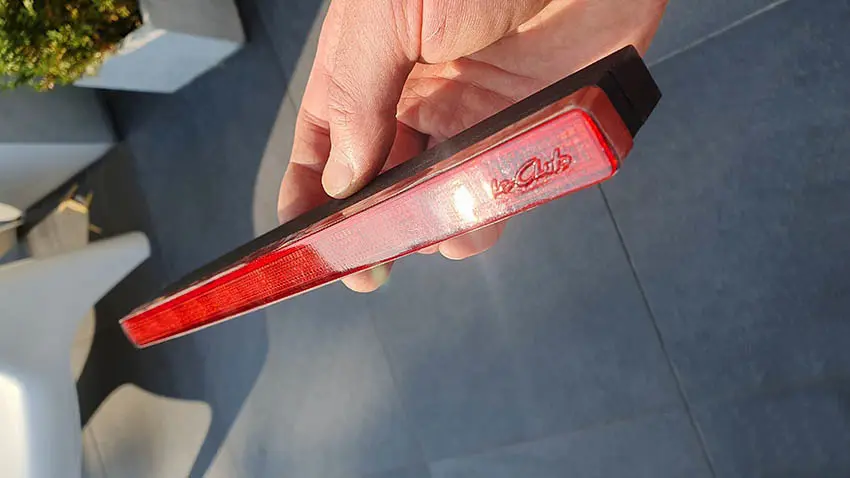