Product | Marine propulsion components |
Technology | Vacuum casting, 3D printing (SLS, SLA) |
Material | PU shore, Epoxy resin, PA12 |
Finish | Mass tining, painting, and silk printing/stickering |
Timeline | 8 days |
Quantity | 7 sets |
Discover our case study on the manufacturing of marine propulsion systems, completed in a record time of 8 days thanks to advanced technologies such as vacuum casting and 3D printing. We produced high-quality components for a client specializing in eco-friendly electric propulsion solutions, now adapted to electric boat engines
About our client
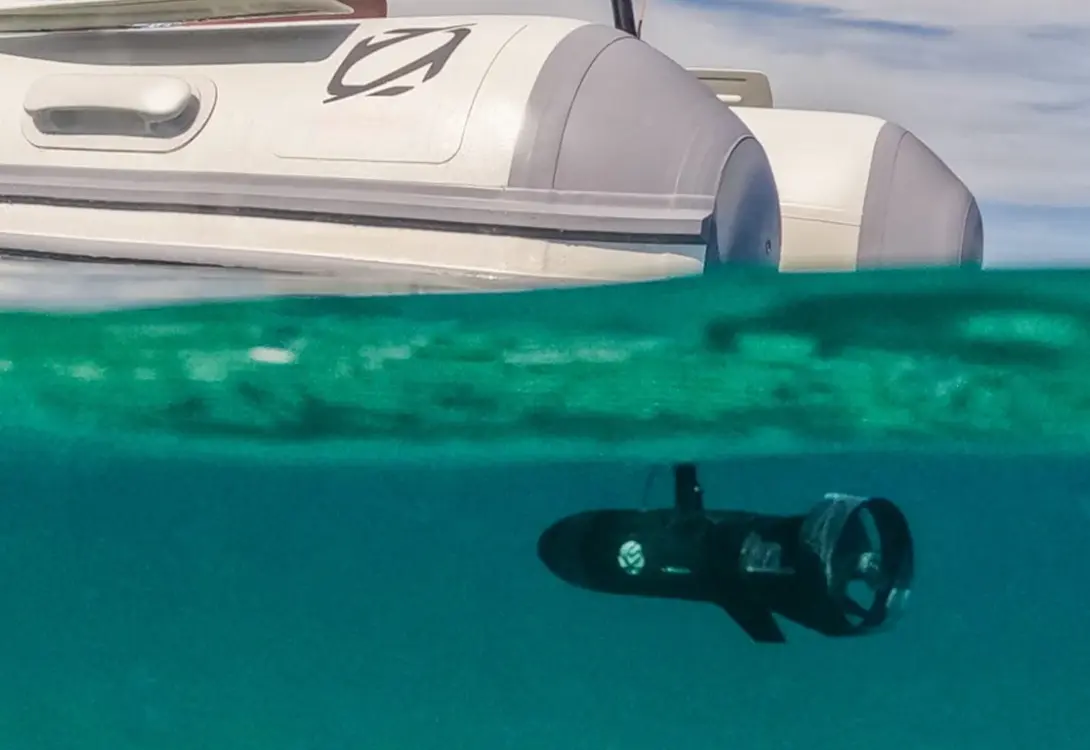
Our customer is dedicated to developing and spreading eco-friendly electric propulsion solutions for watercraft. They initially tested their innovative technology on surf and SUP boards, as well as canoes, and are now adapting it for electric boat motors.
Technical challenges
This project focuses on the manufacturing of marine propulsion systems and components. Employing cutting-edge technologies like vacuum casting and 3D printing (SLS, SLA) with materials such as PU shore, epoxy resin, and PA12, we ensure the production of top-quality marine propulsion systems. Our finishing touches include mass dyed color, painting, and screen printing. The project is slated for completion in just eight days.
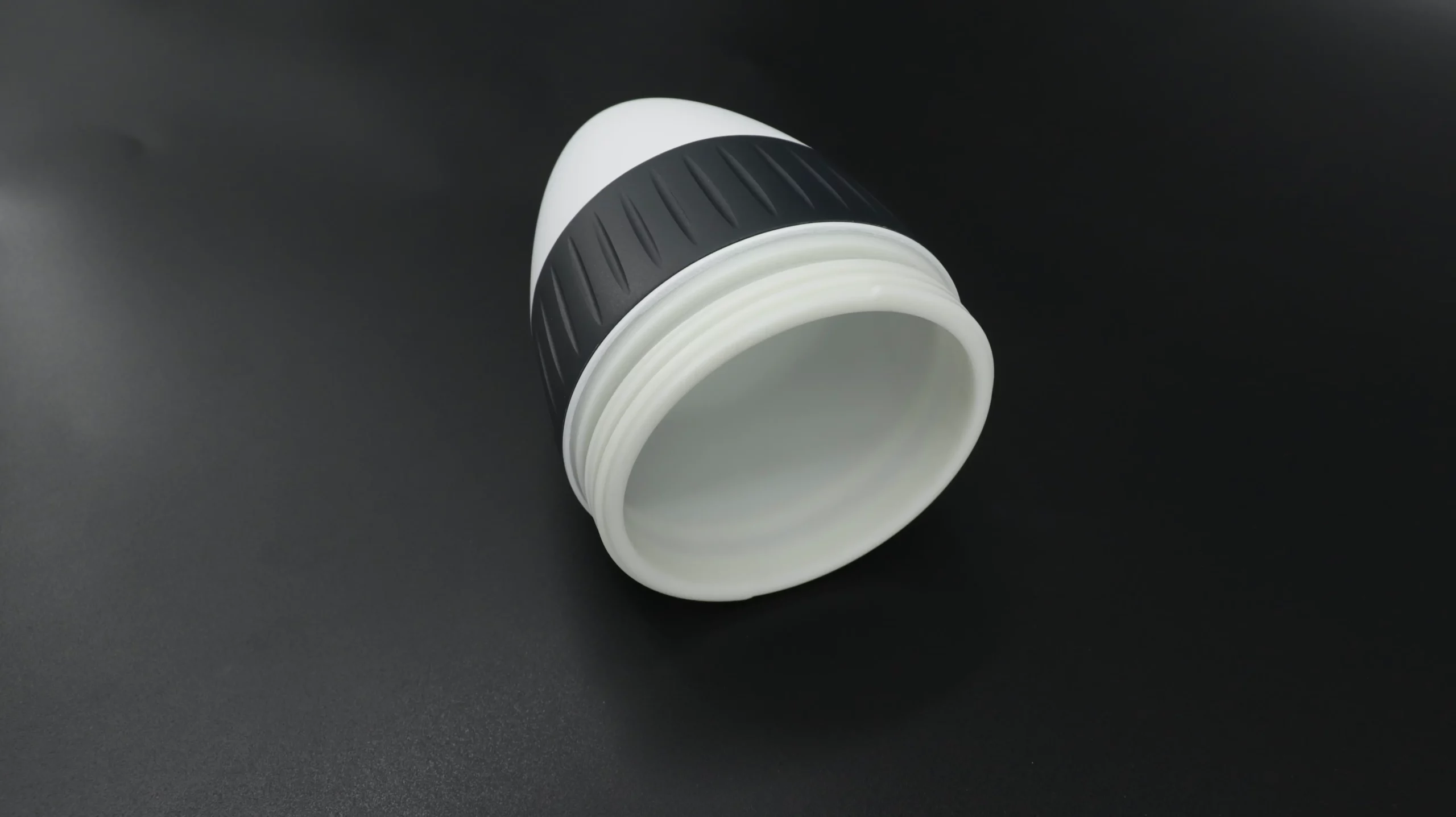
Our solution
Our project delves into the intricacies of the following challenges and explores effective solutions to achieve flawlessly assembled prototypes.
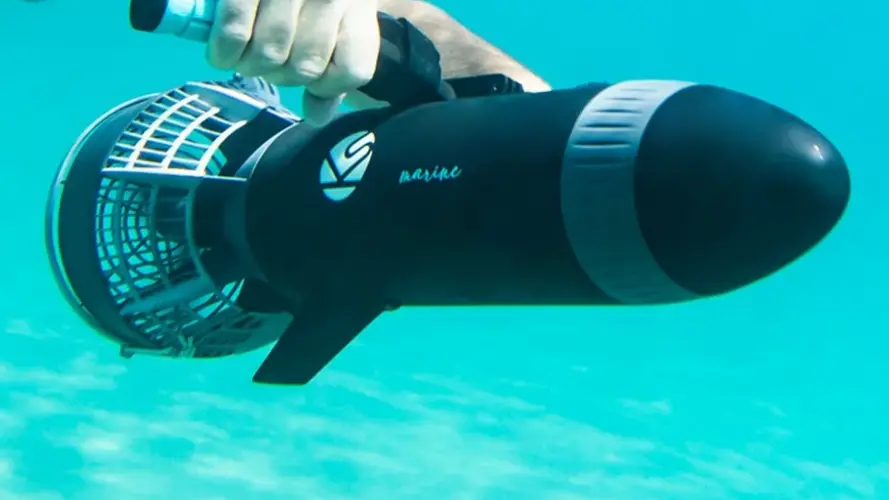
Assembly challenges
In addition, achieving precise assembly of 3D printed and vacuum-casted parts requires strict adherence to 2D plans. To maintain dimensions and quality, we rely on highly skilled technicians with extensive experience in executing these intricate operations.
Physical deformation of the manufactured parts can pose challenges during assembly. To mitigate and reduce this deformation, we employ various post-processing techniques, including manual adjustments, the use of jigs and fixtures, and some anti-deformation methods. In some cases, secondary processing is also utilized to address these issues effectively.
Decoration
Accurate placement of screen-printed logos requires specialized tools and jigs, underscoring the meticulous attention to detail integral to our assembly processes.
Conclusion
This project highlights our expertise in producing high-quality components with precision engineering, even under tight deadlines. By utilizing advanced manufacturing technologies such as vacuum casting and 3D printing, and employing high-performance materials like PU shore, epoxy resin, and PA12, we overcame complex technical challenges to deliver a reliable and eco-friendly solution for marine propulsion systems.
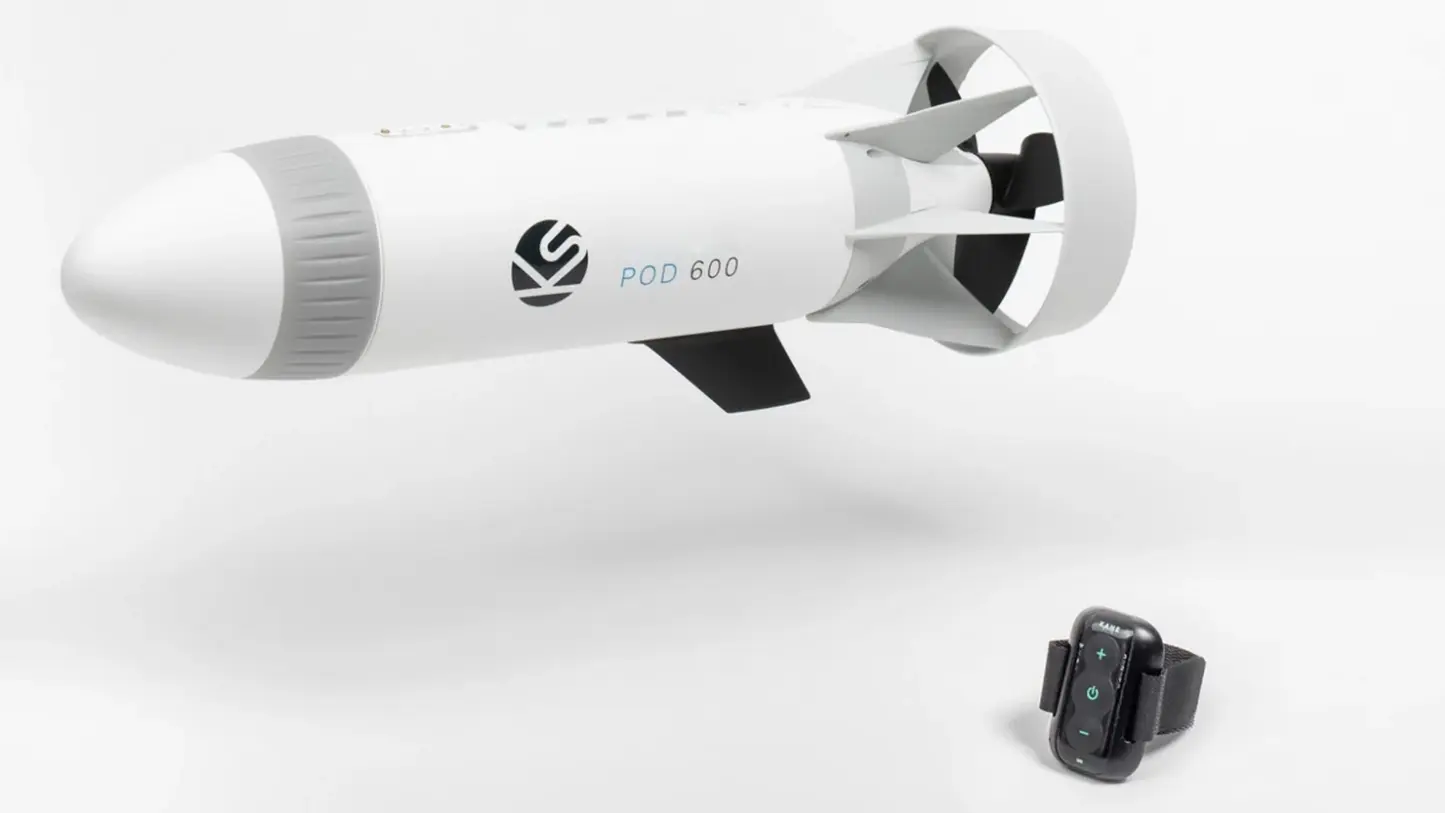
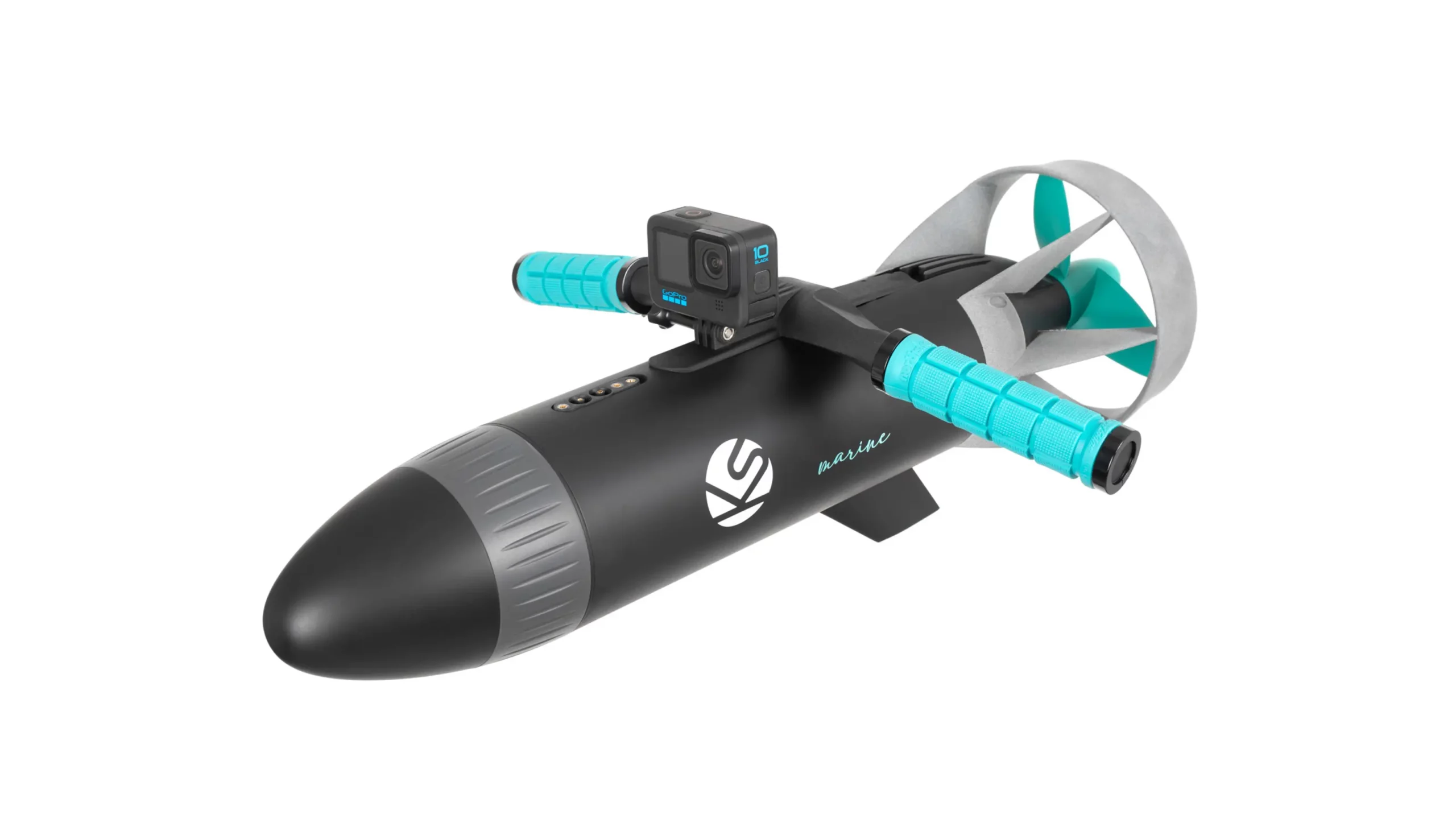