Product | Assembly table |
Technology | CNC metal |
Material | Aluminum 6061, PTFE, ABS |
Finish | As machined |
Timeline | 14 days |
Quantity | 1 set of 62 assembled parts |
This project focused on crafting a specialized assembly table for our client. With precise CNC machining, we created 62 intricate parts, each with unique specifications and over 100 threads.
Attention to detail was key, from assembly design to laser engraving, resulting in a functional and visually appealing final product.
About our client
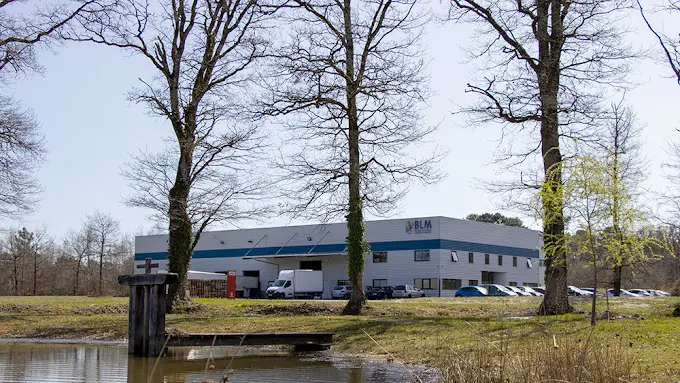
Our client specializes in the construction industry. They offer innovative solutions and a range of products recognized as a benchmark in the electricity and construction markets.
Technical challenges
The production of a set of 62 parts mainly made of plastic and aluminum, required meticulous work and rigorous quality controls.
The table itself was a sizable piece, measuring 1.6 m x 0.8 m / 63 in x 31.5 in, that demanded precision machining on large aluminum plates and the use of high-precision CNC equipment.
Among the 100 threads, there were specific ones like NPT 1/8 (electrical threads), which necessitated customized manufacturing to meet our client’s needs.
The assembly of all these parts involved incorporating positioning elements, assembly clearances, and a poka-yoke system to prevent assembly errors.
The finishing touches included laser engravings on the table for identifying various elements and aiding the operator, along with the polishing of all parts to ensure a visually pleasing appearance and operator safety.
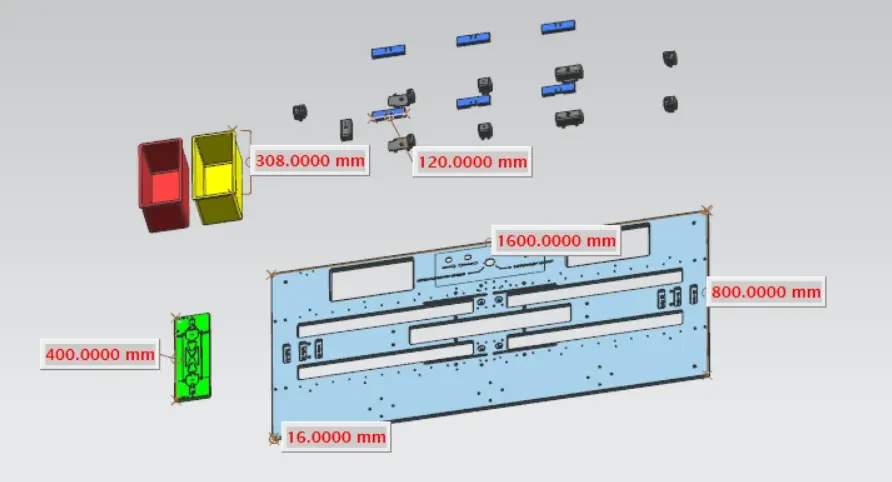
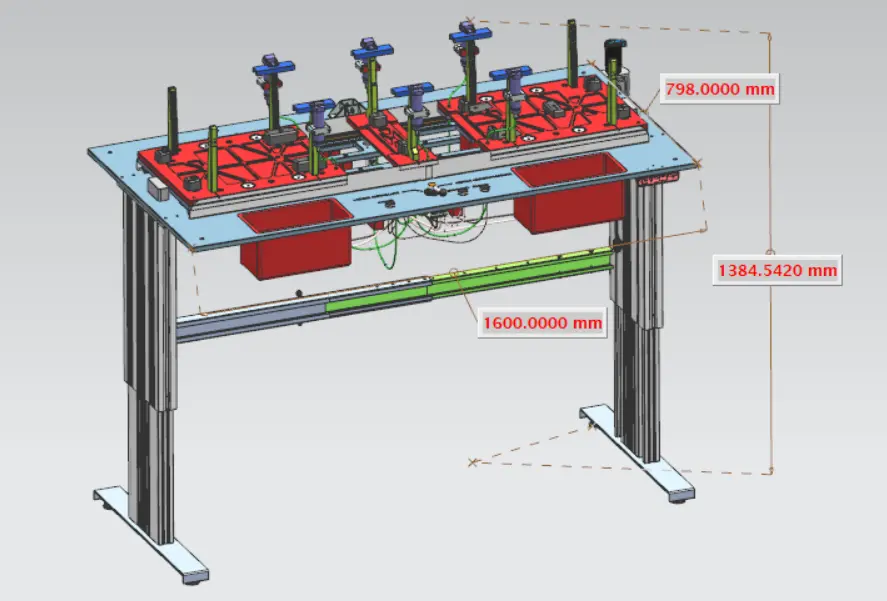
Our solution
To address the technical challenges, our team of experts implemented the following solutions:
- Utilization of high-precision CNC machines for machining aluminum and plastic parts, ensuring tight tolerances and uniform quality.
- Design and integration of positioning and safety devices to facilitate part assembly while minimizing the risk of errors.
- Close collaboration with our client
sto understand their unique needs and adapt our manufacturing process accordingly.
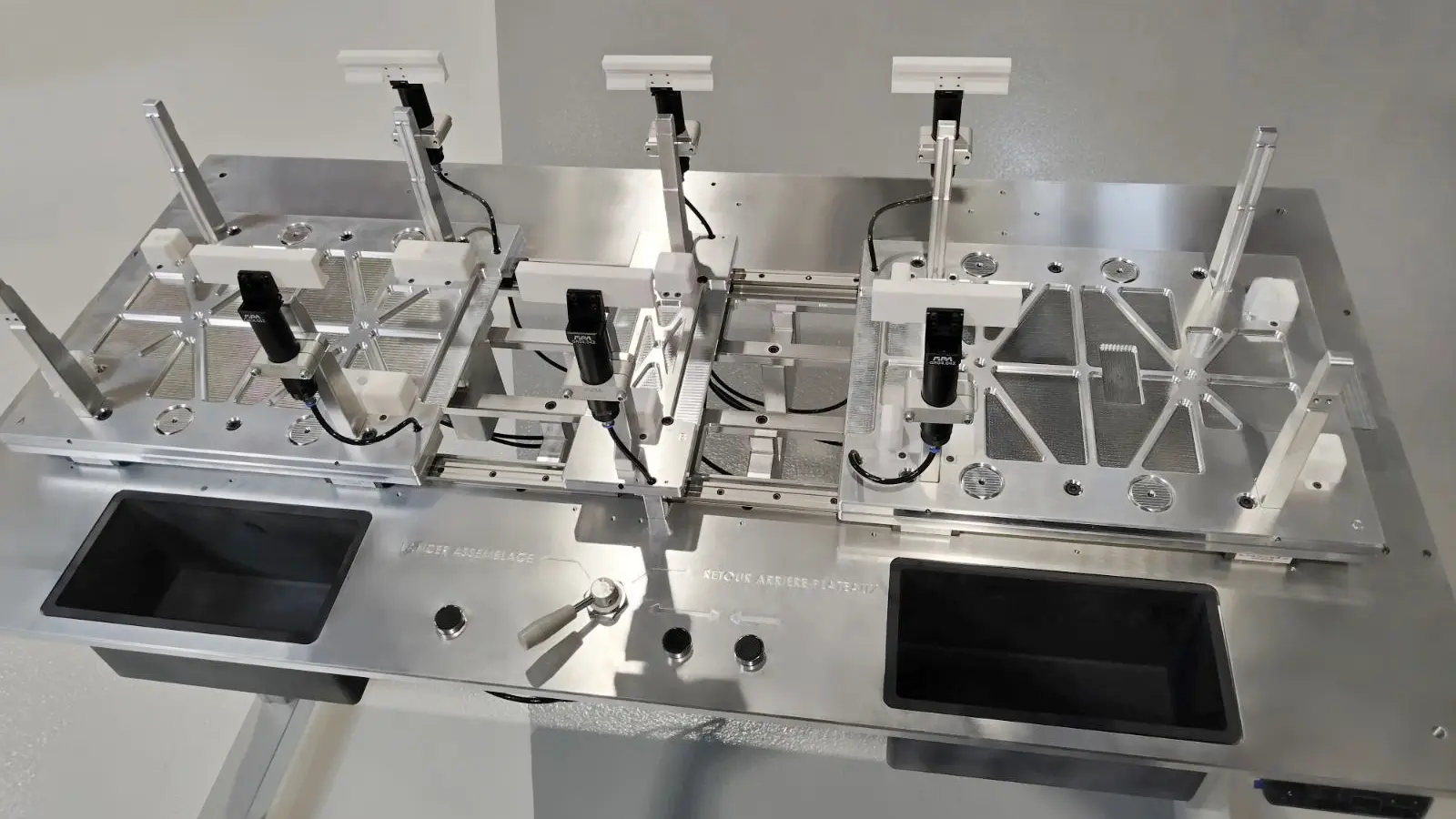
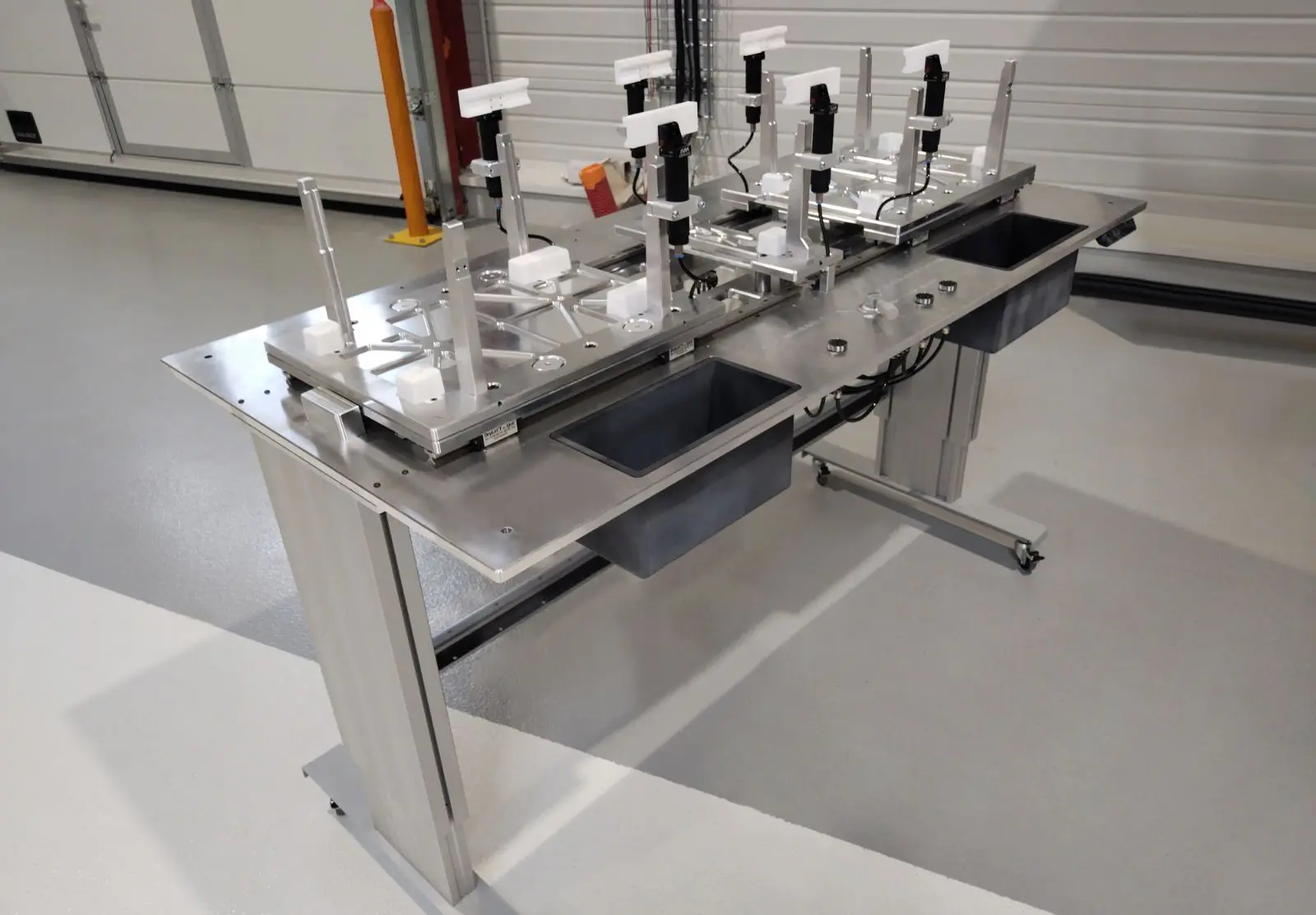
Results
Thanks to our meticulous approach and commitment to excellence, we achieved the following results:
- Successful fabrication and precise assembly of the 62 parts, with perfect compatibility of custom threads.
- Delivery of the table in accordance with the required specifications within the allotted 14 days.
- Positive feedback from our client, highlighting the exceptional quality of work and attention to detail.