Product | Lifting hooks for cranes |
Technology | Compression molding |
Material | Silicone shore 70-80A |
Finish | Mass-Dyeing RAL 5010, Logo engraving |
Timeline | 20 Days |
Quantity | 100 pcs |
This case study delves into the collaborative journey between our customer and Protolis, spanning various manufacturing stages to meet the unique challenges with scaling up the volume of a large, heavy, and structurally complex product.
About our client
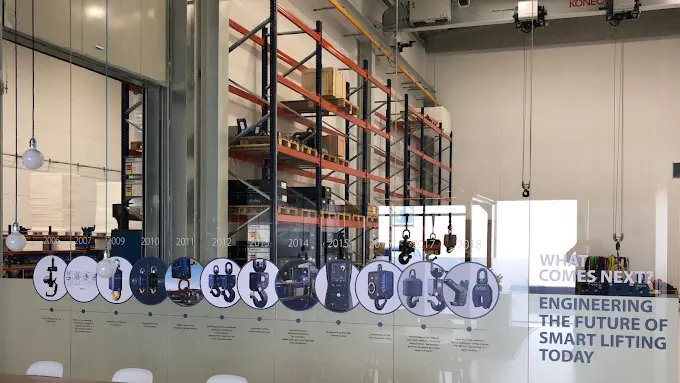
Our client, a Spanish company specializing in lifting solutions for industrial applications, has been collaborating with Protolis for many years, demonstrating a relationship built on trust and ongoing cooperation.
Manufacturing process evolution
The collaboration began with vacuum casting using PU shore for smaller volumes (few dozen). However, limitations arose due to material constraints, particularly in challenging environments involving chemicals, grease, and varying temperatures.
Seeking enhanced mechanical resistance and resilience to oils and temperatures, our customer transitioned to compression molding with silicone.
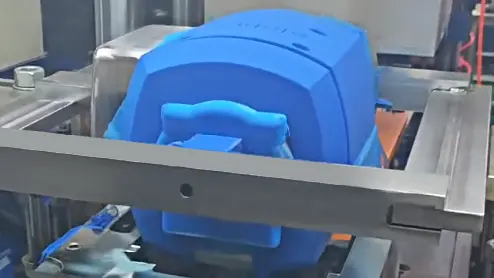
Project challenges
Structural complexity: The product’s substantial size and weight, combined with intricate design elements, presented a unique set of challenges in the manufacturing workflow.
Mold design complexities: Complications arose in the mold design due to the need for undercuts on both the outer and inner walls. Striking a balance between functional requirements and industrial manufacturing constraints proved to be a demanding aspect.
Threaded inserts difficulty: The inclusion of threaded inserts on different sides further heightened the complexity. Since they couldn’t be overmolded, the inserts were mounted after molding, but their pull-out resistance needed to be ensured.
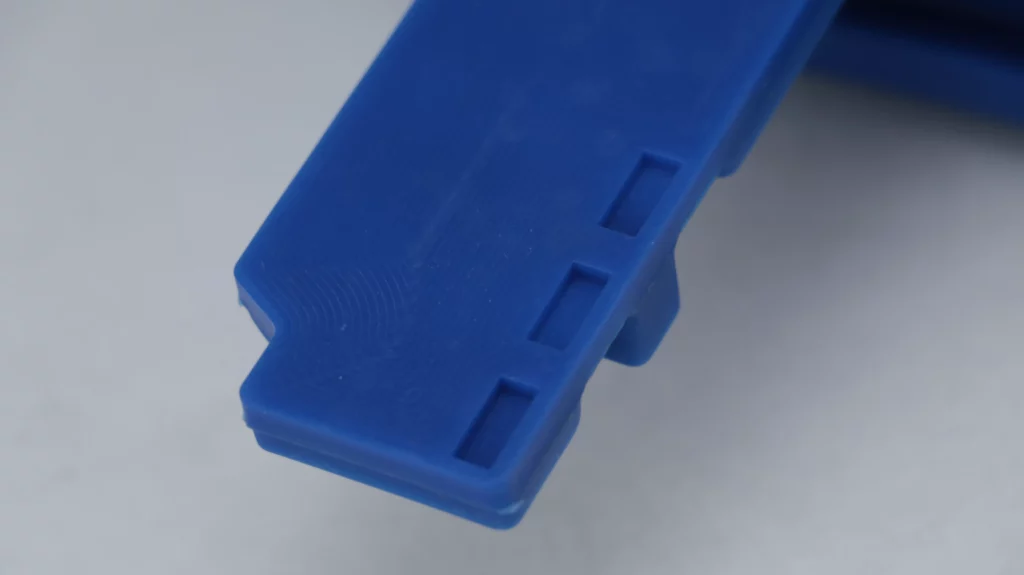
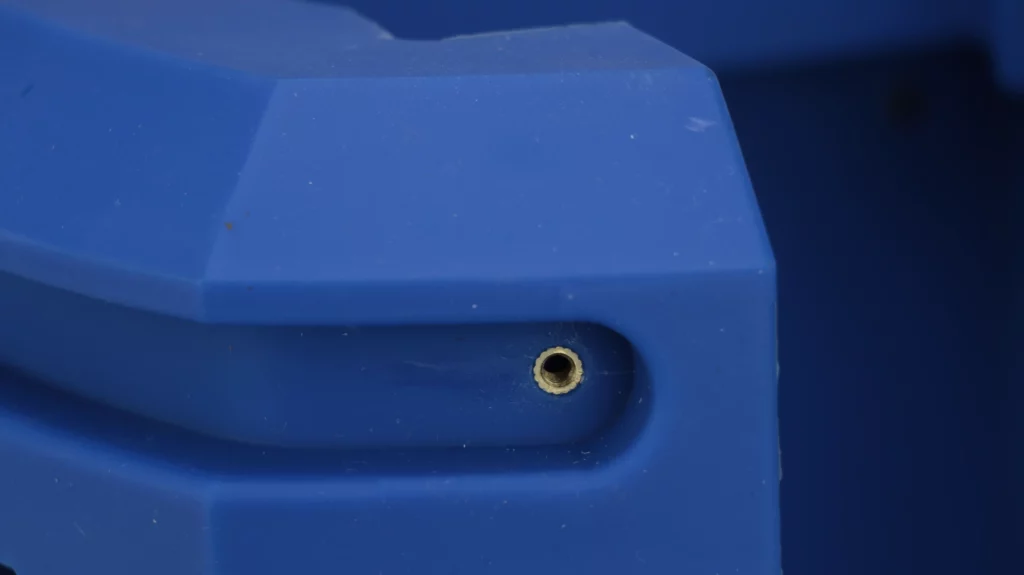
Innovative solutions
To overcome demolding challenges, a teflon treatment was applied to the mold’s interior, facilitating the release of specific parts.
The integration of metal inserts after the piece’s production added additional functionalities, such as screws, magnets, and more.
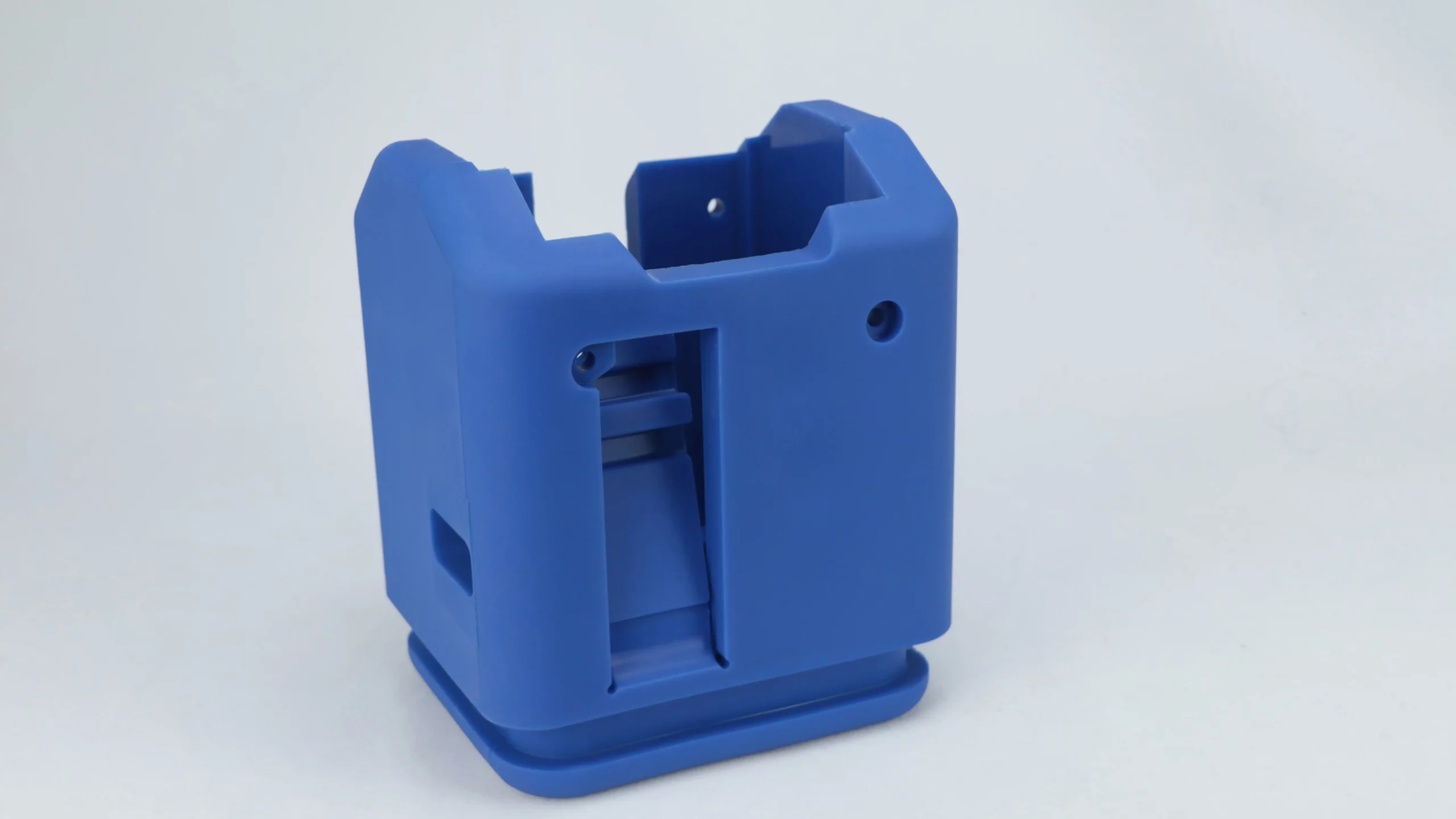
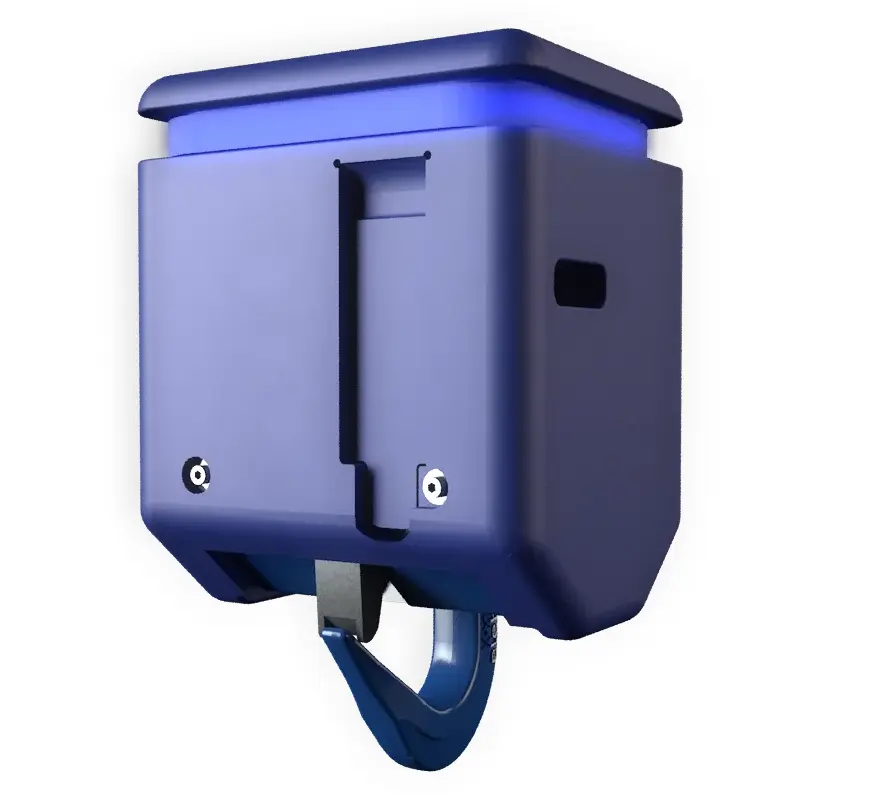
Results
Customer’s collaboration with Protolis resulted in an optimized manufacturing process, overcoming initial material limitations and achieving a complex yet functional design.
The project’s success showcased Protolis’ expertise in addressing multifaceted challenges in large-scale and structurally intricate productions.