Product | Cell Holder for Customized Batteries |
Technology | CNC , Vacuum casting, Rapid injection |
Material | ABS, PUABS V0, PAGF30 |
Finish | Mass dyed, Simple polishing |
Timeline | 16 days/1st Order, 26 Days/2nd Order, 27days/3rd Order |
Quantity | 24 pieces for CNC, 90 pieces for Vacuum Casting, 4000 pieces for Injection Molding |
This is an example of a client who was guided every step of the way by Protolis, from prototyping to low-volume manufacturing to mass production. At each stage, various manufacturing methods were employed, each with its own advantages and challenges.
About our client
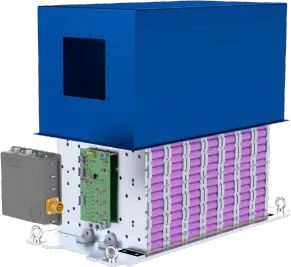
Collaborating with major industrial groups, our client is a key player in the design of innovative energy solutions. They leverage their expertise to provide energy storage systems and customized batteries, meeting the demands of the most challenging sectors such as aerospace and automotive, while actively contributing to the energy transition.
The company takes pride in offering tailor-made solutions, adapted to the specific needs of its clients, with a focus on small series production. Through this approach, it meets the most complex mobility demands, while actively contributing to the transition towards a more sustainable and electrified economy.
Technical challenges and solutions
Depending on the various phases of the project, from prototyping to production, and the resulting quantities, different production processes were considered.
Here is a detailed explanation of each stage, along with the challenges faced and the solutions provided by Protolis:
Stage 1: Prototyping
The first 24 pieces were made using CNC machining in ABS, providing accuracy and speed but at a higher cost.
Challenge and solution: For small quantities (<= 25pc), CNC machining was favored for its speed and high precision despite its higher cost.
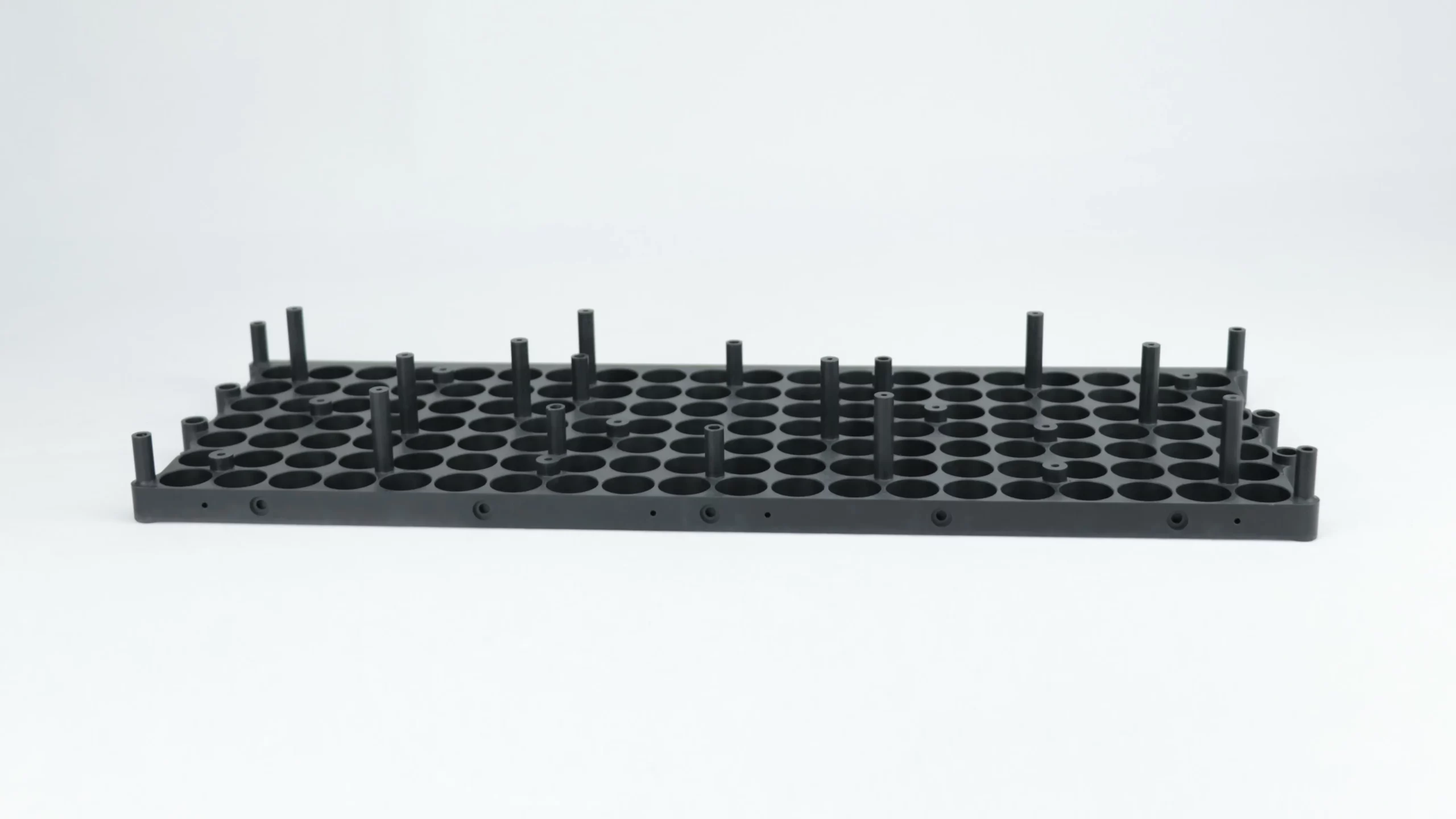
Stage 2: Low-volume manufacturing
For the following 90 pieces, we used vacuum casting manufacturing technology.
Challenges: Vacuum casting proved to be the most complex phase in meeting flatness and tolerances.
Solutions: Measures were taken to control the flatness and tolerance of the 234 holes during the vacuum casting process. The use of jigs helped counteract deformations. Functional control jigs and others for adjusting deformations were created. Rigorous post-production checks were carried out to ensure dimensional tolerances, despite potential variations in the dimensions of the ribs.
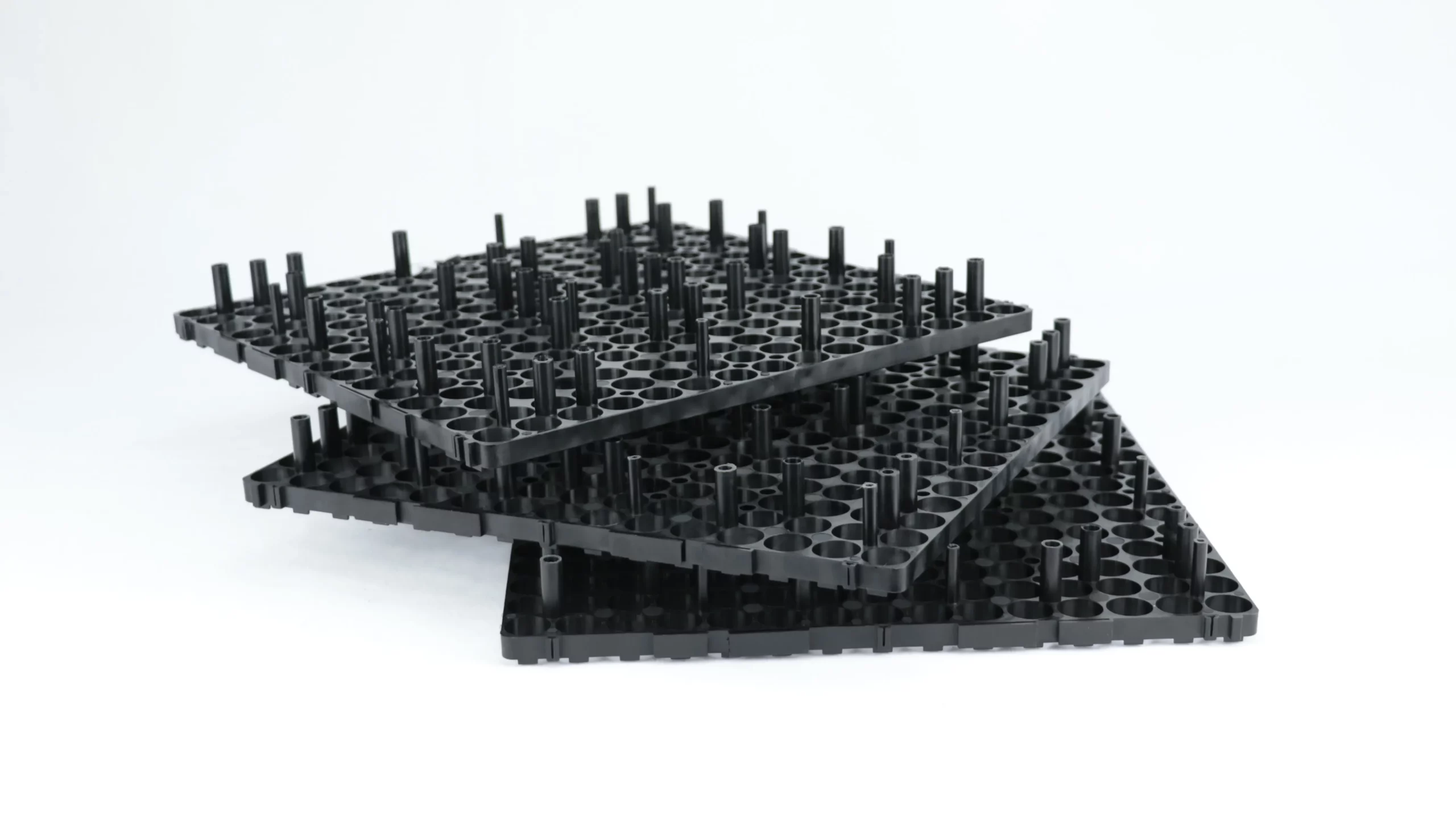
Stage 3: Mass production
For the final production of 4000 pieces, the transition to rapid injection molding was crucial to scale up production while ensuring cost competitiveness.
Challenge: Initial investments are required but pay off as piece costs decrease with increased production volume.
Solutions: Switching to plastic injection offers industrial-quality precision while minimizing deformations. Additionally, adherence to tolerances has significantly improved.

Results
The transition from one technology to another allowed for increased production with controlled costs, stable quality, decreased deformations, all while maintaining satisfactory tolerances.
Transitioning from CNC to vacuum casting resulted in a 60% reduction in production costs. Then moving from vacuum casting to injection molding yielded more than a 90% reduction in production costs, particularly after covering the initial injection tool expenses.
- Successful production scaling from 24 pieces to 4,000 pieces.
- Managed cost-effectiveness by employing varied manufacturing processes at different stages.
- Achieved desired precision and minimized deformations through preparation, careful planning and control measures.
- Guiding our customer through diverse manufacturing challenges.
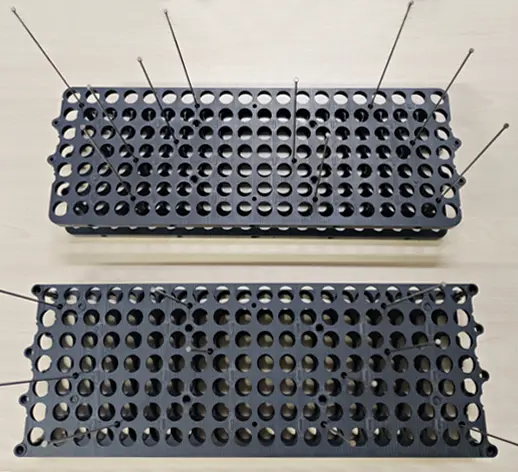